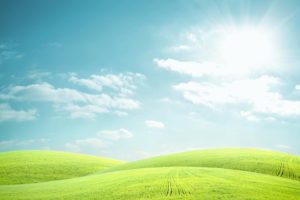
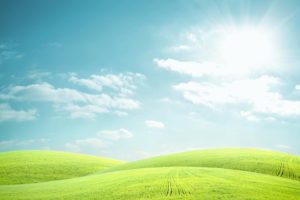
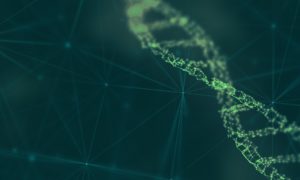
OpGen: Leadership in the global fight against the AMR pandemic
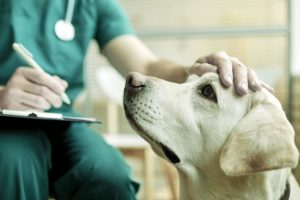
Volition signs global supply agreement for Nu.Q Vet Cancer Test
…as is the number of fishers and fish farmers
The total number of fishers and fish farmers globally has been on an upward trend as more people living in coastal areas turn to fishing and aquaculture to sustain their livelihoods.What are the alternatives to preserve sustainability?
The fish space encompasses both private and listed companies. Mitsubishi Corp is present in the fishing industry though, as a conglomerate, only some of its value can be ascribed to its fish business (which is part of its Food division). As investors consider how to invest in industries committed to sustainability, and are increasingly measuring the environmental, social, and governance (ESG) aspects, they are likely to focus on elements of the food production industry that offer alternatives. Plant-based foods are proliferating (as discussed in our note on meat alternatives) and in aquaculture there are many approaches. These include energy conservation, enhanced environmental measures and improved farming practices. Novel scientific approaches such as the production of cultured fish and seafood are also being developed. Cellular fish (cell-based production) could solve many environmental and sustainability issues, but its three main challenges are: (1) viability of the technology on a commercial scale, (2) cost and (3) consumer acceptance and the regulatory environment. There are a number of companies looking to launch novel fish and seafood products, such as BlueNalu and Shiok Meats on the cell-based side and Nestlé and New Wave Foods looking to launch plant-based seafood alternatives.Environmental regulatory support
The sustainability of the fish industry and moves to research and produce alternative sources are underpinned by global and regional environmental directives such as the UN SDG (Sustainable Development Goals) 14, to ‘conserve and sustainably use the oceans, seas and marine resources.’An efficient source of protein
Fish is a relatively efficient source of protein, as its feed conversion ratio is lower than that of any traditionally farmed meat. Cattle is the most inefficient source of protein, as it takes a substantial amount of feed and water (and land) for each kilogram or calorie of meat. In addition, it takes a significant amount of time to rear the animals before they can be slaughtered. In this respect, fish is more efficient.Sustainability is important to consumers
Environmental concerns have come to the fore over the last decade and consumers demand more sustainable products. Fishing is no exception, with consumers now trying to avoid species that are at risk and fish that is not sustainably caught or farmed. This should help to effect lasting change within the industry, as suppliers adapt to satisfy growing consumer concerns.
|