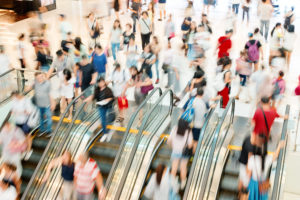
Consumer watch
Consumer watch: Bargains galore Consumer sectors continue to face the twin headwinds of low consumer confidence/likely lower demand and inflationary cost pressures. The pressures on
“Edison’s accessible and high-quality research gives us the opportunity to communicate an independent perspective of Tyman to a wide variety of potential stakeholders.”
Consumer watch: Bargains galore Consumer sectors continue to face the twin headwinds of low consumer confidence/likely lower demand and inflationary cost pressures. The pressures on
Subscribe PDF Follow Extracting value from the new issue slump A toxic cocktail of slowing growth, rising inflation and belatedly hawkish central banks has resulted
Subscribe PDF Follow Related Content Vaccines: Niche no longer Despite fits and starts, scientists remain fully invested in discovering curative vaccines. The complexity of the
Steel making is an energy (mainly from coal and electricity) intensive industry. For each ton of carbon steel produced, 1.83t of CO2 is emitted. Annually, it contributes 5% to C02 global emissions and the only way to reduce these is to improve steel-making efficiencies, maximize the use of scrap and use or develop new technology.
Globally, coal contributes more than 40% of fossil fuel emissions, followed by oil (35%) and the balance from gas. The main industrial sectors of release are electricity and heat production (50%), transport (20%), and the manufacturing and construction industries (20%). Roughly 50% of all emissions worldwide stems from five countries, namely China (25%), the United States (12%), India (6%), Russia (4%) and Japan (3%). (Source: United States Environmental Protection Agency.)
Simplistically, steel production is either based on iron ore, produced via blast furnace and an oxygen converter, or via an electric arc or electric induction process, based largely on scrap metal. The latter has a major advantage as it is a cleaner steel-making process, with estimated emission savings of 40% relative to the blast furnace process.
Increasing use of electric arc capacity will gradually reduce steel industry emissions. Meanwhile, measures to encourage the use of scrap by way of export and pricing controls by a number of producing countries will have the effect of securing steel scrap reservoirs in domestic markets. This should help keep scrap costs at economic levels, making its future use for lower emission steel production more attractive.
The input consumption parameters listed by the World Steel Association to produce 1,000kg of liquid steel, are 1,370kg iron ore, 780kg metallurgical coal, 270kg fluxes (the minerals that increase the fluidity of slag) and 125kg scrap via the blast furnace/oxygen route. The electric arc route consumes 586kg iron ore, 150kg metallurgical coal, 88kg fluxes and 7 10kg scrap.
Scrap plays a key role in suppressing industry emissions and resource consumption, as every ton of scrap used for steel production circumvents the emission of 1.5t of CO2 and the consumption of 784kg of iron ore, 630kg of coal and 182kg of limestone. Putting it differently, to make steel using scrap consumes only a quarter of the energy otherwise needed by using iron ore.
Currently at 1.8bnt, global steel production consists of 73% via the blast furnace/oxygen process, while electric steel-making provides only 27% of the volume. Some 20 years ago, the ratio was 74:26, indicating that actual capacity growth came via the oxygen (iron ore) route. This was mainly because the steel-making capacity explosion came from China, which expanded capacity from around 180mtpa to 1,100mtpa in 2020, a growth rate of almost 10% pa, with 97% of the additions via the iron ore route. The rest of the world grew its capacity over the same period by less than 1% pa. However, looking at only the last five years, a period where electric steel-making became very popular, iron ore-based capacity grew by less than 3% pa, while electric steel making grew at 5% pa.
Although electric steel-making capacity expansions were a relatively small part of global additions earlier on, this greener route of steel-making has gained popularity over the more recent past. The graph below shows the change in global output of electric steel-making over the last 20 years per region (China shown separately). Although Chinese growth in electric steel-making over the 20-year period was strong (+340%), its relevance fades in comparison with its growth in iron ore-based capacity of 644% and growth in an iron ore-sourced industry which was already 2.5x larger at the start. The ratio of electric steel-making compared to iron ore-based steel-making in China is now 1:10. Therefore, the Chinese capacity explosion in blast furnace/oxygen steel-making far outweighed the increase in electricity-based capacity in other regions. As a matter of interest, countries that have specifically targeted the electric route over the last 20 years are Italy (now 85% reliant on electric steel-making), the United States (71%), India (56%) and Russia (32%).
‘Looking at the different raw material consumption rates for producing steel via the electric route compared to the oxygen process, the former has a major advantage as a cleaner steel-making process. An immediate emission saving of 40% seems possible and, if the recent trend to add steel-making capacity to the electric route is maintained, the benefit will grow relative to the other process.’
Evolution in electric steel making output (mtpa)
Source: World Steel Association
Although electric arc furnaces can also utilise iron ore and other resources containing iron, in almost in all cases scrap is the preferred source for this process. Across the world, about 650mt of steel products, including used steel cans, appliances, automobiles and construction materials, are recycled every year. This equates to a worldwide carbon steel supply ratio of 35% sourced from recycling and 65% from other iron-bearing resources such as iron ore. China sources only 20% of its iron demand for steel-making from scrap, while Turkey consumes 86%, the United States 70% and the EU around 56%. In South Africa, some 4.0mt are recycled annually, which is a ratio of 44% compared to steel production.
World trade in steel scrap is around 100mtpa, with Europe being the most active, handling about 50% of both imports and exports. The main net exporting steel scrap countries, in 2020 were the United States (12mt), Germany (4mt), Japan (7mt), the UK (6mt) and the Netherlands (3mt). The main net importers were Turkey (22mt), India (7mt), Belgium (4mt), Pakistan (4mt), Spain (3mt) and South Korea (3mt). Europe (including the UK) exported almost 50mt of steel scrap in 2020, while simultaneously importing 55mt.
It is therefore no surprise to see the EU currently promoting export controls over scrap, proposals for which are being finalised. Many other countries have also realised the benefits of preserving domestic iron reservoirs through the introduction of export controls, including, in some cases, blanket bans on the export of steel scrap. In South Africa, the government recently extended its controls by another two years as it feels that although the initial actions were effective, there is further to go in fully achieving its target of creating an adequate supply of quality scrap at a cost benefit. The government also added an ad valorem duty of 20%, as well as additional physical controls to secure further leakage. (See SA scrap reservoir protected themes report.)
Subscribe to receive related Metals & mining content
Get access to the very latest content matched to your personal investment style.
This website uses cookies so that we can provide you with the best user experience possible. Cookie information is stored in your browser and performs functions such as recognising you when you return to our website and helping us understand which section of the website you find more interesting and useful. See our Cookie Policy for more information.
These cookies are used to deliver our website and content. Strictly necessary cookies relate to our hosting environment, and functional cookies are used to facilitate social logins, social sharing and rich-media content embeds.
Advertising Cookies collect information about your browsing habits such as the pages you visit and links you follow. These audience insights are used to make our website more relevant.
Please enable Strictly Necessary Cookies first so that we can save your preferences!
Performance Cookies collect anonymous information designed to help us improve the site and respond to the needs of our audiences. We use this information to make our site faster, more relevant and improve the navigation for all users.
Please enable Strictly Necessary Cookies first so that we can save your preferences!